How long a corrosion inhibitor is used to clean a well?
The duration for which a corrosion inhibitor, such as NOCORGREEN WELL™ or other industry-standard inhibitors, is used to “clean” or protect a well from corrosion depends on factors such as
- the application method
- well conditions
- the specific goals of the maintenance job (e.g., mitigating existing corrosion or preventing future corrosion)
The term “clean” in this context likely refers to protecting the well from corrosion-related damage or removing corrosion byproducts during maintenance, so I’ll address both protection and remediation.
Below is a detailed explanation based on the previous analysis of NOCORGREEN WELL™ and general oilfield corrosion inhibition practices.
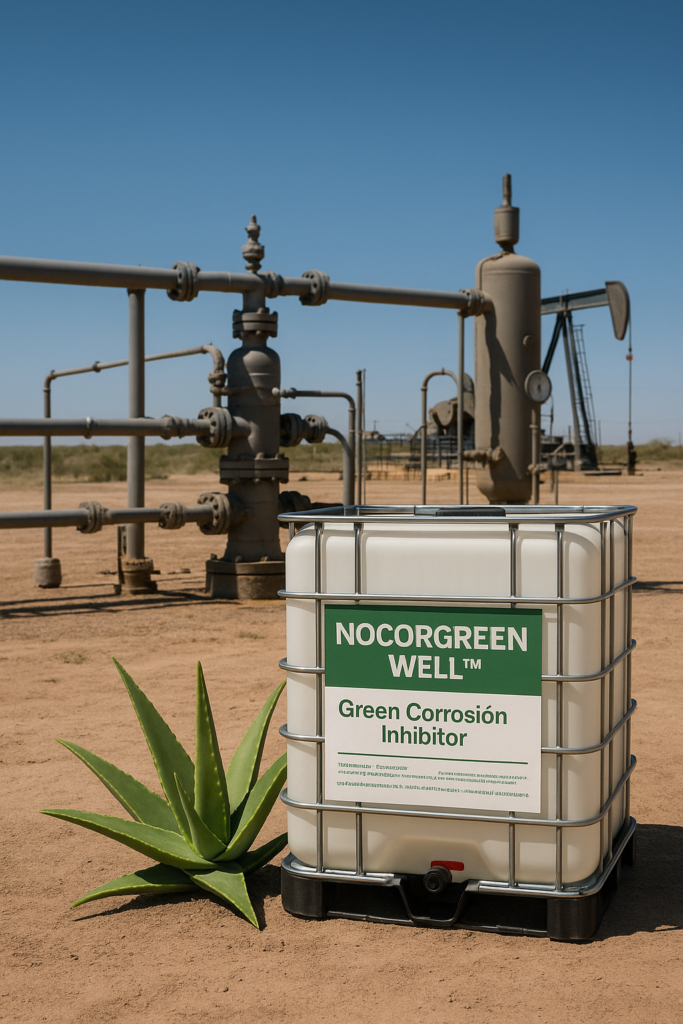
Duration of Corrosion Inhibitor Use in a Well
1. Corrosion Protection (Preventive Maintenance)
Corrosion inhibitors are primarily used to prevent corrosion rather than “clean” existing corrosion. However, their application can be part of a maintenance job to protect well components (e.g., casing, tubing) from further degradation. The duration depends on the application method:
- Batch Treatment (Squeeze Treatment):
- Application Process:
- Injection: The inhibitor, such as NOCORGREEN WELL™, is injected into the well annulus or formation, typically diluted (e.g., 5–40% concentration in water or hydrocarbon solvent). This takes a few hours to a day, depending on the well volume and pump capacity.
- Flush: A brine or water flush (1,000–10,000 liters) follows to distribute the inhibitor, taking additional hours.
- Shut-in Period: The well is shut in for 6–24 hours to allow the inhibitor to adsorb onto metal surfaces or reservoir rock, forming a protective film.
- Protection Duration: Once applied, the inhibitor provides corrosion protection for 6 months to 2 years, depending on:
- Inhibitor type (e.g., aloe-based polysaccharides in NOCORGREEN WELL™ form a persistent film).
- Well conditions (e.g., temperature, water cut, CO₂/H₂S levels).
- Production rates (higher water production may deplete the inhibitor faster).
- Example: NOCORGREEN WELL™, with its film-forming properties, may last 6–12 months per batch treatment, based on its design for harsh downhole environments.
- Application Process:
- Continuous Injection:
- Process: The inhibitor is injected continuously into the wellbore or flowlines using a metering pump at low concentrations (e.g., 5–20 ppm for NOCORGREEN WELL™ or similar products).
- Duration: This is an ongoing process during well production, lasting as long as the well is active or corrosion risks persist (potentially years). Dosage is adjusted based on water chemistry and corrosion monitoring.
- Maintenance: Injection systems require periodic checks (e.g., weekly or monthly) to ensure proper dosing and system functionality.
- Encapsulated Inhibitors:
- Process: When inhibitors are available in encapsulated form, they are deployed for slow release, typically during stimulation or completion phases.
- Duration: Protection lasts several months to years, depending on the release rate and reservoir conditions. Reapplication occurs when corrosion rates increase.
2. Cleaning Existing Corrosion (Remediation)
If the goal is to “clean” a well by addressing existing corrosion or its byproducts (e.g., iron oxides, scale deposits linked to corrosion), corrosion inhibitors are used in conjunction with other chemicals or mechanical methods. The duration for this process includes:
- Chemical Cleaning (Descaling/Acidizing):
- Process: Corrosion byproducts like iron oxides or scale (e.g., calcium carbonate) are often removed using acid treatments (e.g., hydrochloric acid, citric acid) or chelating agents. A corrosion inhibitor like NOCORGREEN WELL™ is added to protect metal surfaces during acidizing, as acids can exacerbate corrosion.
- Duration: The cleaning process takes a few hours to 1–2 days, depending on:
- The severity of corrosion or scale buildup.
- The volume of acid or cleaning solution (e.g., 50–500 barrels).
- The need for soaking or circulation (typically 4–12 hours).
- Role of Inhibitor: During cleaning, the inhibitor is applied simultaneously (e.g., 0.1–1% concentration in the acid solution) to prevent further corrosion, with no extended shut-in required for this phase.
- Post-Cleaning Inhibition:
- After cleaning, a corrosion inhibitor is applied to prevent future corrosion, using batch treatment or continuous injection (as described above).
- Duration: Protection lasts 6 months to 2 years for batch treatments or ongoing for continuous injection, similar to preventive maintenance.
3. Factors Affecting Duration
- Well Conditions: High temperatures (>150°C), high water cut, or elevated CO₂/H₂S levels may reduce inhibitor longevity, requiring more frequent reapplication.
- Inhibitor Type: NOCORGREEN WELL™, with its aloe-based formulation, is designed for harsh environments but may have varying retention compared to synthetic inhibitors (e.g., imidazolines). Its biodegradability may necessitate more frequent application in some cases.
- Production Dynamics: High flow rates or water production can deplete inhibitors faster, shortening protection duration.
- Corrosion Severity: Wells with heavy corrosion may require initial cleaning followed by more frequent inhibitor applications.
4. Typical Timeframes
- Preventive Maintenance:
- Batch Treatment: Application takes 1–2 days (including shut-in); protection lasts 6 months to 2 years.
- Continuous Injection: Ongoing during production, with daily to weekly adjustments.
- Encapsulated Inhibitors: Protection for months to years, with application during well completion or workovers.
- Corrosion Cleaning (Remediation):
- Cleaning Process: Hours to 2 days for acidizing or chemical flushing.
- Post-Cleaning Protection: 6 months to 2 years (batch) or ongoing (continuous).

Best Practices for Using Corrosion Inhibitors in Well Maintenance
Here are key recommendations to optimize corrosion inhibition during a maintenance job:
- Pre-Maintenance Assessment:
- Analyze water chemistry (CO₂, H₂S, chlorides, pH) and corrosion rates using probes or coupons.
- Confirm NOCORGREEN WELL™’s compatibility with well metallurgy (e.g., API N80, L80) and other chemicals (e.g., acids, scale inhibitors).
- Cleaning Existing Corrosion:
- Use acidizing or chelating agents (e.g., 15% HCl with 0.1–1% NOCORGREEN WELL™) to remove corrosion byproducts or scale. Circulate for 4–12 hours, depending on buildup severity.
- Flush the well with brine to remove residues post-cleaning.
- Applying NOCORGREEN WELL™:
- Batch Treatment: Inject NOCORGREEN WELL™ (5–40% concentration) into the annulus, followed by a brine flush. Shut in for 6–24 hours. This is cost-effective for wells with moderate corrosion risks.
- Continuous Injection: Install a metering pump for ongoing injection (5–20 ppm) in high-water-cut wells. Use automation (e.g., WellAware systems) for precise dosing.
- Encapsulated Form: Deploy encapsulated inhibitors during workovers for long-term protection.
- Monitoring and Follow-Up:
- Install corrosion monitoring tools (e.g., linear polarization probes, coupons, etc.) to track inhibitor performance.
- Test produced fluids for inhibitor residuals (via HPLC) to ensure adequate protection.
- Reapply batch treatments every 6–12 months or adjust continuous injection based on monitoring data.
- Environmental Considerations:
- Leverage NOCORGREEN WELL™’s eco-friendly profile to comply with regulations, especially in offshore or sensitive areas.
- Ensure proper disposal of produced water per local guidelines.
Specific Notes on NOCORGREEN WELL™
- Duration Estimate: Aloe-based inhibitors like NOCORGREEN WELL™ typically provide 6–12 months of protection per batch treatment, based on their film-forming mechanism. Continuous injection is ongoing as needed.
- Limitations: There is some limitations on high-temperature performance (>150°C) or compatibility with acidizing fluids. In these cases, contact us for precise dosing and application guidelines.
- Advantages: Its plant-based, biodegradable nature makes it ideal for environmentally sensitive operations, and its efficacy against CO₂ and H₂S corrosion aligns with common oilfield challenges.
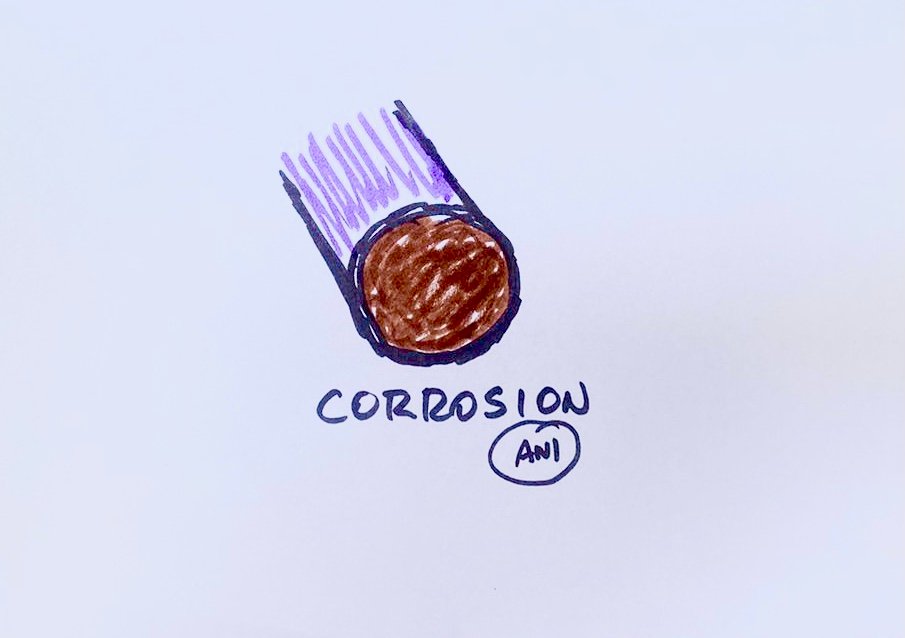
Summary of Durations
- Cleaning Existing Corrosion: Hours to 2 days for chemical cleaning, with NOCORGREEN WELL™ added to protect during the process.
- Preventive Corrosion Inhibition:
- Batch Treatment: 1–2 days to apply, protects for 6 months to 2 years.
- Continuous Injection: Ongoing, with daily/weekly adjustments.
- Encapsulated Inhibitors: Months to years, applied during workovers.
- Recommendation: For a maintenance job, combine a chemical cleaning (if corrosion byproducts are present) with a batch treatment of NOCORGREEN WELL™ for long-term protection. Use continuous injection for high-risk wells.
If you have specific well conditions (e.g., temperature, water cut, or corrosion type) or need further details on NOCORGREEN WELL™’s application, please contact with us.
