Central Processing Facilities (CPFs): Engineering the Critical Node in Upstream Hydrocarbon Systems.
Central Processing Facilities (CPFs) are engineered installations that serve as the initial point of conditioning and treatment for multiphase production fluids in upstream oil and gas developments.
By performing critical phase separation, fluid stabilization, and metrological functions, the CPF enables downstream transportation and commercialization of hydrocarbons in accordance with design and regulatory specifications.
🔬 Functional Overview
🛢️ 1. Inlet System and Flow Assurance
CPFs typically interface with wellhead platforms, satellite gathering systems, or flowlines. Inlet manifolds are designed with provisions for slug handling, pigging, and sand management. Front-end flow assurance measures address hydrate mitigation (via methanol/glycol injection), emulsion control, and solid transport through line conditioning.
⚗️ 2. Three-Phase Separation and Degassing
A combination of high- and low-pressure horizontal separators, free-water knockouts, and electrostatic treaters is used for primary separation. These vessels are configured for optimal retention time, level control, and internals that support effective disengagement of phases:
- Crude oil is routed to stabilization and quality assurance systems.
- Associated gas is compressed or treated as per sales gas spec or reinjection strategy.
- Produced water undergoes primary treatment before reinjection or discharge.
- Solids, including formation sand, are collected via desanders, with appropriate erosion and disposal controls.
🧪 3. Fluid Conditioning and Product Specification
- Crude oil treatment typically involves desalting, dehydration via electrostatic coalescers, and pressure-temperature stabilization to meet BS&W and RVP thresholds.
- Gas systems include triethylene glycol (TEG) dehydration, H₂S removal through amine contactors, molecular sieves for deep drying, and gas compression.
- Produced water treatment integrates API separators, induced gas flotation units (IGF), and filtration packages to meet local environmental standards.
📊 4. Metering and Custody Transfer
High-accuracy fiscal metering stations (e.g., Coriolis or ultrasonic meters) and representative sampling systems are installed to comply with API MPMS, ISO 3171, and OIML R117 standards. These systems are calibrated and validated under ISO 9001 and local regulatory protocols.
🔄 5. Export and Utility Integration
- Oil export is facilitated via booster pumps or LACT units feeding into storage tanks or transmission pipelines.
- Gas may be compressed for transportation via pipeline or for conversion in FLNG systems.
- Produced water is routed for subsurface reinjection or surface discharge in compliance with reservoir management strategies and environmental legislation.
⚙️ Key Engineering Considerations
- Modular Design: Enables flexible deployment in onshore and offshore contexts, with scalability based on production profiles.
- Instrumentation and Control: Integrated with SCADA, DCS, and ESD systems for real-time operational control and functional safety.
- Reliability Engineering: Focus on uptime KPIs via condition-based monitoring (CBM), rotating equipment diagnostics, and predictive maintenance.
- Integrity Management: Employs NACE-compliant material selection, corrosion inhibition programs, and internal inspection regimes.
🧭 Strategic Relevance of CPFs
A well-optimized CPF:
- Serves as the fulcrum for enhanced oil recovery (EOR) and gas monetization strategies
- Ensures early-stage compliance with product specifications and environmental criteria
- Reduces downstream processing complexity and associated OPEX
- Enhances reservoir economics by maintaining production continuity and minimizing flaring or venting
Chemicals Used at a CPF are not Eco Friendly
Central processing facilities in the oil and gas industry utilize a wide range of chemicals for various purposes including processing, treatment, and transportation of hydrocarbons.
These chemicals are essential for enhancing production, preventing corrosion, controlling flow assurance issues, and ensuring safe and efficient operations.
Most of these products may be harmful, toxic and with carcinogenic effects to human beings, and all of them are contaminant and dangerous to the environment. Instead, you can use Aloetrade America green and sustainable solutions for use at a CPF.
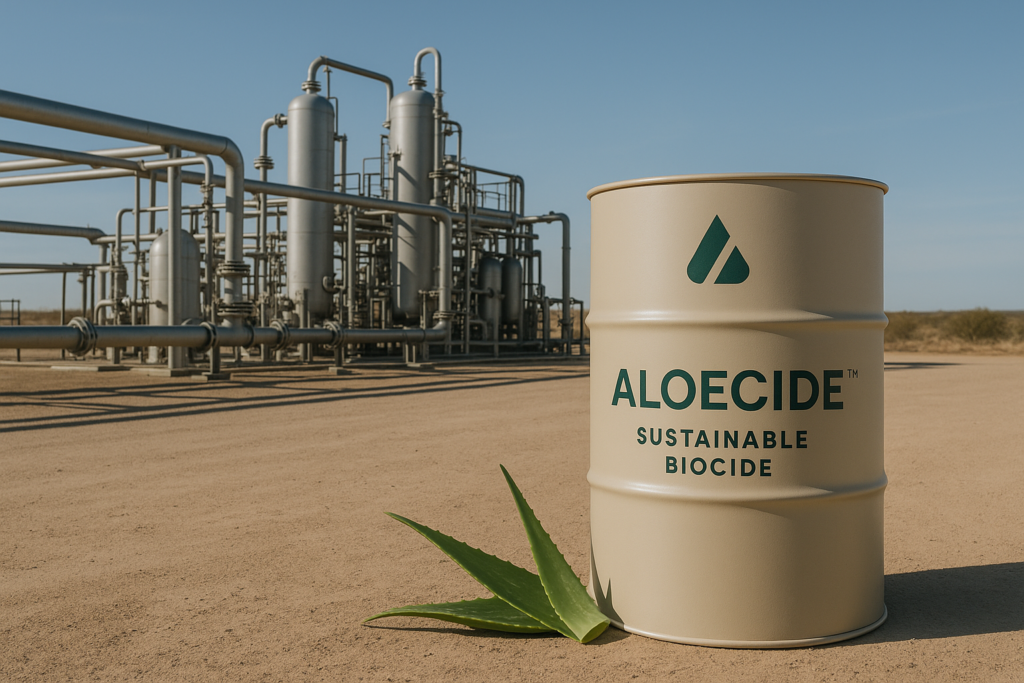
We offer plant based solutions -made with aloe and other natural extracts- to be used in the oil & gas industry.
All products are made with renewable resources. Biodegradable solutions. Non toxic products. No harmful products. Green and sustainable products. All these products are used and validated by the oil and gas industry. These green and sustainable products are environmentally friendly solutions for CPFs.
Or contact to us.
