This article describes the best suggestions for a maintenance job to inhibit corrosion in an oil well.
These recommendations integrate the use of NOCORGREEN WELL™ where applicable and address broader corrosion management strategies.

1. Assess Well Conditions and Corrosion Risks
- Water Chemistry Analysis: Conduct a comprehensive analysis of produced water to identify corrosive agents (e.g., CO₂, H₂S, chlorides, oxygen) and their concentrations. Measure pH, salinity, and temperature to determine the corrosivity level.
- Well Environment: Evaluate downhole conditions, including temperature (e.g., 250°F–550°F for high-temperature wells), pressure, and flow regime, as these influence inhibitor selection and application.
- Material Assessment: Identify the metallurgy of well components (e.g., API N80, L80, or Super-13 steel) to ensure compatibility with NOCORGREEN WELL™ or other inhibitors.
- Corrosion Monitoring: Install corrosion monitoring tools (e.g., linear polarization probes, coupons) to establish baseline corrosion rates and track inhibitor effectiveness over time.
2. Select NOCORGREEN WELL™ for Eco-Friendly Corrosion Inhibition
- Why Choose NOCORGREEN WELL™: Its plant-based formulation (aloe-derived polysaccharides and anthraquinones) forms a protective film on metal surfaces, making it effective against CO₂ and H₂S-induced corrosion. Its eco-friendly nature aligns with regulatory and sustainability goals, especially in environmentally sensitive areas.
- Application Suitability: Use NOCORGREEN WELL™ in wells with moderate to high corrosion risks due to acidic gases or saline water, particularly in production or stimulation phases. It’s ideal for operators seeking green alternatives to traditional inhibitors like imidazolines or phosphonates.
- Compatibility Testing: Before application, test NOCORGREEN WELL™ for compatibility with other chemicals (e.g., scale inhibitors, biocides, or acidizing fluids) to avoid emulsions or reduced efficacy.
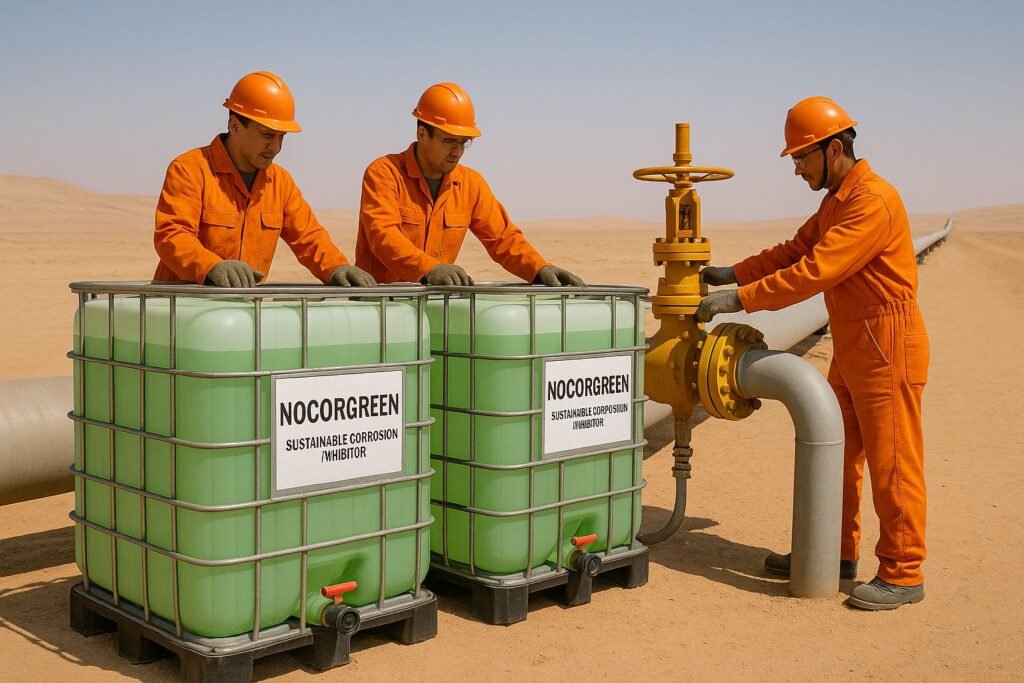
3. Choose an Appropriate Application Method
- Batch Treatment (Squeeze Treatment):
- Process: Inject NOCORGREEN WELL™ into the well annulus between the casing and tubing, followed by a flush (e.g., 1,000–10,000 liters of water or brine) to distribute the inhibitor to the producing zone. Shut in the well for 6–24 hours to allow adsorption onto metal surfaces.
- Duration: Batch treatments with NOCORGREEN WELL™ can provide corrosion protection for 6 months or more, depending on well conditions and inhibitor retention.
- Advantages: Cost-effective for wells with stable production and lower water cuts. The aloe-based inhibitor’s film-forming properties may enhance long-term protection.
- Procedure:
- Dilute NOCORGREEN WELL™ (e.g., 5–40% concentration in a hydrocarbon solvent or water) based on manufacturer guidelines.
- Inject into the annulus using a chemical injection pump.
- Flush with brine or water to ensure even distribution.
- Resume production, allowing the inhibitor to mix with produced fluids gradually.
- Continuous Injection:
- Process: Use a metering pump to inject NOCORGREEN WELL™ continuously into the wellbore or flowlines at a low concentration, adjusted based on water cut and corrosivity.
- Duration: Ongoing during production, with regular adjustments based on corrosion monitoring data.
- Advantages: Suitable for high-water-cut wells or those with severe corrosion risks. Automation (e.g., WellAware systems) can optimize injection rates based on flow meter data.
- Procedure:
- Install a chemical injection system with a flow meter to monitor water flow rates.
- Set injection rates to achieve target concentrations.
- Monitor residuals in produced fluids using high-pressure liquid chromatography (HPLC) to ensure consistent dosing.
- Encapsulated Inhibitors:
- Process: Consider encapsulated versions of NOCORGREEN WELL™ (if available) for slow-release applications, reducing the need for frequent treatments.
- Duration: Protection can last months to years, depending on release rates and well conditions.
- Advantages: Ideal for remote or subsea wells where frequent intervention is impractical.
4. Integrate with Other Corrosion Control Methods
- Material Selection: Use corrosion-resistant alloys (e.g., Super-13, C-110 grade steel) for critical components like tubing or casing to complement chemical inhibition.
- Cathodic Protection: Install sacrificial anodes (e.g., magnesium) near buried pipelines to reduce galvanic corrosion, especially for surface equipment.
- Coatings: Apply plastic or epoxy coatings to surface pipes and tanks to provide an additional barrier against corrosion.
- Oxygen Scavengers: If oxygen is a significant corrosion driver, combine NOCORGREEN WELL™ with oxygen scavengers to reduce corrosivity.
5. Address Scale and Other Corrosive Factors
- Scale Inhibition: Since scale (e.g., calcite, barite) can exacerbate corrosion by creating crevices or altering flow dynamics, use a compatible scale inhibitor (e.g., STOPSCALE™ the aloe-based scale inhibitor from Aloetrade) alongside NOCORGREEN WELL™.
- Acidizing Considerations: During well stimulation with acids (e.g., hydrochloric acid), ensure NOCORGREEN WELL™ or a specialized acidizing inhibitor (e.g., propargyl alcohol-based) is used to protect against acid-induced corrosion.
- Biocide Treatment: If microbiologically influenced corrosion (MIC) is a concern, apply biocides to control sulfate-reducing bacteria, ensuring compatibility with NOCORGREEN WELL™. Try ALOECIDE™
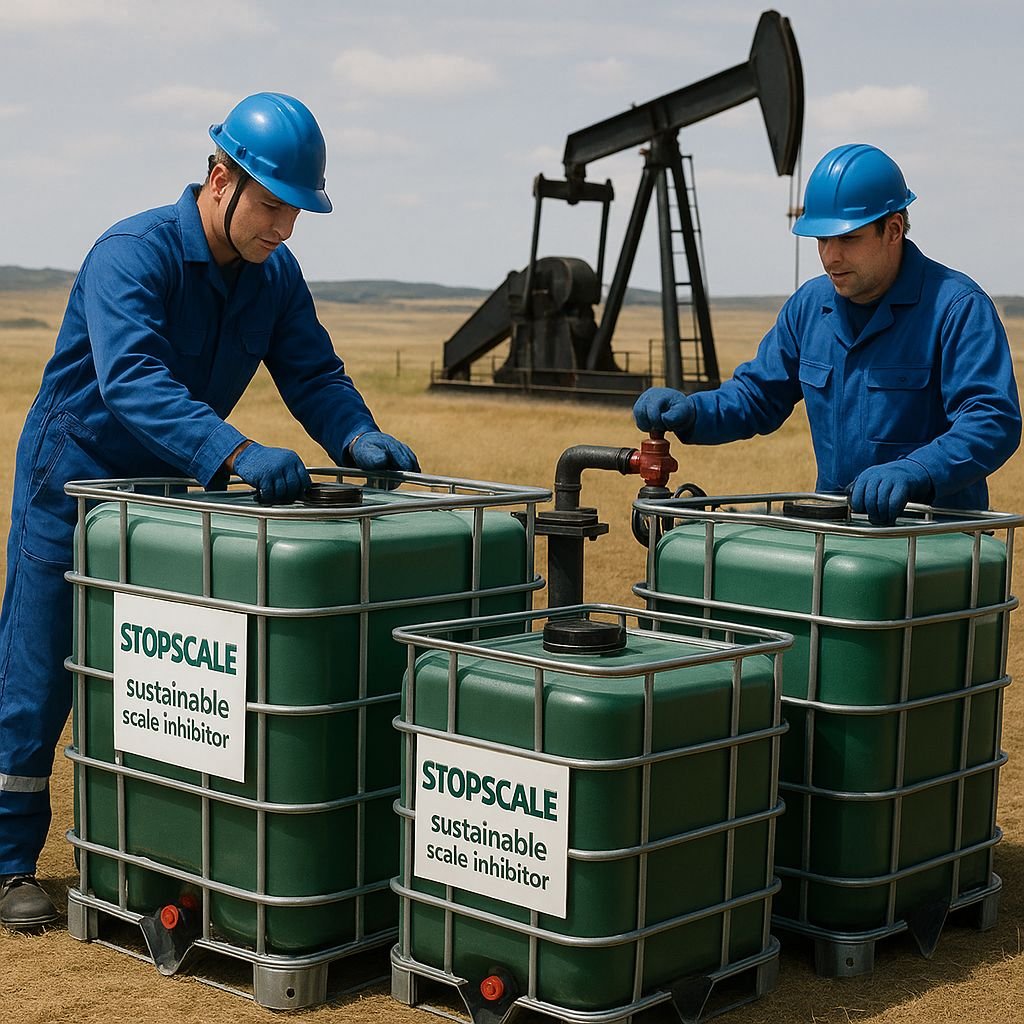
6. Automate and Monitor Inhibitor Performance
- Automation: Use automated chemical injection systems (e.g., WellAware) to maintain precise inhibitor concentrations based on real-time flow and water cut data. This prevents under- or over-dosing, which can lead to corrosion or emulsions.
- Monitoring: Regularly measure corrosion rates using linear polarization, weight loss coupons, or electrochemical sensors. Analyze produced fluids for inhibitor residuals to confirm effective dosing.
- Maintenance Schedule: Schedule maintenance based on monitoring data:
- For batch treatments, reapply every 6–12 months or when corrosion rates increase.
- For continuous injection, adjust dosages weekly or monthly based on water chemistry changes.
7. Environmental and Safety Considerations
- Leverage Green Chemistry: Prioritize NOCORGREEN WELL™ for its environmental benefits, especially in regions with strict regulations (e.g., offshore operations). Its biodegradability reduces disposal concerns compared to traditional inhibitors.
- Safe Handling: Ensure workers are trained in handling and injecting NOCORGREEN WELL™, following safety data sheets (SDS) provided by Aloetrade America LLC.
- Regulatory Compliance: Verify that NOCORGREEN WELL™ meets local environmental standards for produced water disposal, particularly in sensitive ecosystems.
8. Economic and Operational Optimization
- Cost-Effectiveness: Batch treatments with NOCORGREEN WELL™ may reduce costs compared to continuous injection by extending treatment intervals. Field data suggest batch treatments can lower corrosion rates even with less flush volume than conventional inhibitors.
- Workover Planning: Schedule corrosion inhibitor application during routine workovers to replace tubing, pumps, or sucker rods, minimizing downtime.
- Supplier Collaboration: Work with Aloetrade America LLC or their manufacturing partner (Maken Proyectos Industriales SA de CV) for technical support on dosing, application, and performance optimization.
Best Practices Summary
- Preferred Method: Use batch treatment with NOCORGREEN WELL™ for wells with moderate corrosion risks and stable production, as it offers long-term protection (6–12 months) and aligns with the product’s film-forming properties. For high-water-cut or severe corrosion scenarios, opt for continuous injection with automated dosing.
- Complementary Measures: Combine NOCORGREEN WELL™ with scale inhibitors, oxygen scavengers, and cathodic protection to address multiple corrosion drivers.
- Monitoring and Automation: Implement real-time corrosion monitoring and automated injection systems to optimize inhibitor performance and reduce operational costs.
- Sustainability Focus: Leverage NOCORGREEN WELL™’s eco-friendly profile to meet environmental regulations and reduce ecological impact, especially in sensitive areas.
Additional Notes
- Contact Aloetrade: For specific dosing recommendations, application protocols, or compatibility data, contact Aloetrade America LLC directly.
- Field Testing: Conduct a pilot test with NOCORGREEN WELL™ in a representative well to validate its performance under specific conditions before full-scale deployment.
By integrating NOCORGREEN WELL™ with these industry-standard practices, you can effectively manage corrosion in oil wells while prioritizing sustainability and operational efficiency.